Inhalt
- Zuverlässigkeit und Effizienz
- #1: Zu spät kommen
- #2: Das Dach ist undicht
- #3: EMV-Störungen haben keinen Rückwärtsgang
- #4: Pigtails – Hauptgrund für EMV-Probleme
- #5: Spaghettata im Schaltschrank
- Fehlende EMV-Schulung und Sensibilisierung
EMV im Maschinenbau: Ein unverzichtbarer Faktor für Zuverlässigkeit und Effizienz
Stellen Sie sich vor, eine hochmoderne Produktionsanlage steht plötzlich still. Maschinen versagen, Prozesse kommen ins Stocken, und die Produktionsziele rücken in weite Ferne. Die Ursache? Elektromagnetische Störungen, die unvorhersehbare und kostspielige Probleme verursachen. Diese Szenarien sind kein Science-Fiction, sondern reale Herausforderungen, mit denen viele Techniker im Maschinenbau konfrontiert werden.
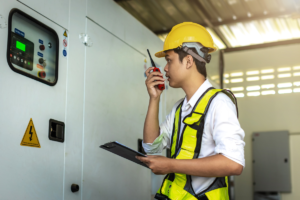
Elektromagnetische Verträglichkeit (EMV) spielt eine entscheidende Rolle in der Maschinenbauindustrie. Sie sorgt dafür, dass elektronische Systeme störungsfrei nebeneinander arbeiten können. Ohne eine sorgfältige Berücksichtigung der EMV-Richtlinien können Maschinen nicht nur ineffizient, sondern auch gefährlich sein. EMV-Probleme führen zu teuren Produktionsausfällen, Sicherheitsrisiken und gesetzlicher Nichtkonformität.
In diesem Blogartikel werden wir die fünf häufigsten EMV-Design-Fehler im Maschinenbau betrachten und zeigen, wie Sie diese vermeiden können.
Fehler #1: Zu spät kommen
Wir haben eine Idee, einen Projektplan, einen Kundenwunsch, eine Innovation. Meist gut geplant, manchmal auch eine hauruck-Übung.
Durchstarten, keine Zeit verlieren – der erste Prototyp soll so schnell wie möglich fliegen!
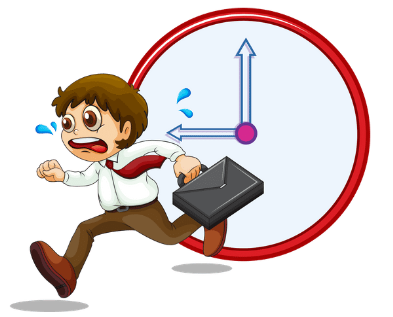
Allmählich kommt dieses und jenes dazu, die parallel laufende Anforderungsanalyse bringt immer wieder neue Kundenwünsche ans Licht und die Termine geraten unter Druck.
❓ Wer denkt da schon an das notwendige Übel mit der elektromagnetischen Verträglichkeit?
⚡Und dann kommt die EMV-Störung. ⚡
Viele Maschinenbauer kennen das:
Tage oder Wochen gehen verloren, Entwicklungsingenieure und Servicetechniker versuchen, das Problem zu lösen, Filterkomponenten werden beschafft, Kabel geschirmt und vielleicht noch ein Consultant involviert.
Irgendwann ist das Problem tatsächlich behoben und als Schlussfolgerung bleibt eine Sammlung von Halbwahrheiten und Massnahmen, die dann beim nächsten Mal irgendwie berücksichtigt werden. Die teuren Notmassnahmen fliessen in die Serienproduktion ein und treiben die Herstellkosten unnötig in die Höhe. Niemand wird je den Mut haben, solche Massnahmen wieder abzuschaffen, denn welche waren wirklich nötig und welche nicht?
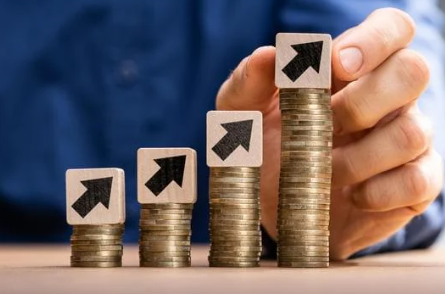
Die meisten EMV-Stolperfallen könnten mit einer praktischen Grundlagenschulung der Beteiligten und einer kurze Analyse durch einen EMV-Berater bereits in einer frühen Entwicklungsphase entdeckt und umgangen werden.
Was wäre denn ein schlaues Vorgehen?
- Jetzt:
Gemeinsame Praxisschulung aller Beteiligten - Wenn Leistungsmerkmale bekannt:
Skizziertes Anlagenlayout mit erfahrener Person besprechen (Antriebssysteme, Steuerschränke, Sensorik) - Elektroschema steht:
Mit EMV-Experte besprechen, Stolperfallen entdecken, Schirmungs- und Erdungsmassnahmen checken - Prototyp gebaut:
Inspektion durch EMV-Experten, allenfalls Precompliance-Messung, Verdrahtungsschwächen entdecken - Prototyp in realistischem Betrieb:
EMV-Messung durch Labor: Im ersten Anlauf durchkommen!
Fehler #2: Das Dach ist undicht
Wenn es plötzlich Probleme gibt mit EMV-Störungen, dann merkt man dies meist auf Grund von Symptomen.
👩⚕️ So wie ein fiebersenkendes Medikament oder eine Schlaftablette nur teilweise und kurzfristig helfen, so ist es auch bei der elektromagnetischen Verträglichkeit.
🔌 Wenn die Temperaturanzeige schwankt, wird das Kabel gewechselt, ein Dämpfungsferrit angebracht oder in der Software beschönigt.
Spinnt das Touchpad, probiert man andere Hersteller aus und wenn der Regler zittert, muss ein Tiefpass in den Regelkreis.
Dies ist Fehler#2: Symptombekämpfung
💧 Das ist, als würde man bei einem undichten Dach in jedem Zimmer des Hauses die Decken mit Silikon abdichten. Das funktioniert auch…bis es woanders reintropft – und irgendwann geht gar nichts mehr – der Zufall oder Murphy entscheiden, wann es soweit ist.
🥇 Aus diesen Gründen lautet die goldene Regel bei der EMV:
Zuerst die Störer ausfindig machen, diese sauber verdrahten und vielleicht entstören.
Dazu gehören korrekt konfektionierte Kabelschirme (bei den Störern immer beidseitig 360°), durchgängig verbundene Kabelkanäle und EMV-fähige Masseverbindungen zwischen Chassis, Kabelkanälen, Umrichtern und Netzfiltern.
Fehler #3: EMV-Störungen haben keinen Rückwärtsgang
Praktisch jedes Gerät, jede Maschine und jede Anlage hat heute irgendwelche Frequenzumrichter und damit Störquellen mit an Bord.
Schnelle Schaltflanken auf den Umrichterausgängen koppeln kapazitiv auf benachbarte Leitungen, den Kabelschirm und häufig auf einen Motor ein.
♨ Diese Störungen wollen zwar zurück zur Quelle, aber nicht auf dem Weg, auf dem sie gekommen sind.
Wer würde schon gerne eine Wanderung machen mit gleichem Hin- und Rückweg? Die EMV-Störungen machen eine Rundtour!
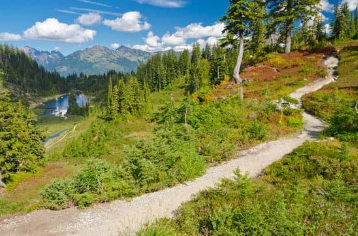
🔌 Wenn alle Leitungen zwischen Anlagenteilen geschirmt geführt würden, dann wäre eine Personenschutzerde dieser Teile genügend. In Wirklichkeit werden aber durch Umrichterleitungen und Motoren Commonmode Störungen in das Anlagenchassis eingekoppelt, die zurück zum Filter des Umrichters müssen.
Sind die Anlagenteile nicht niederinduktiv verbunden UND sämtliche Kabel nahe bei diesen Verbindungen geführt, so werden die Rückströme in alle möglichen Leitungen eingekoppelt.
Insbesondere Busleitungen, Sensorkabel und DC-Speisungen, welche über mehrere Anlagenteile geführt werden, sind dadurch stark gefährdet. Und hat man den Müll dann mal auf dem 0V und auf der 24V Speisung, dann ist er überall.
❗ Die Leitungen zwischen Anlagenteilen sollten wenn möglich in Kabelkanälen geführt werden. So können die Rückströme im Kanal zurückfliessen und spannen gegenüber den Kabeln keine Flächenantenne auf. Wichtig dabei ist, dass die Kanäle bei den Übergangsstellen gut miteinander verbunden werden. Die Hersteller bieten dazu die passenden Verbindungskomponenten an. Die Investition in solche vermeintlichen Kleinteile ist 🥇 Gold wert!
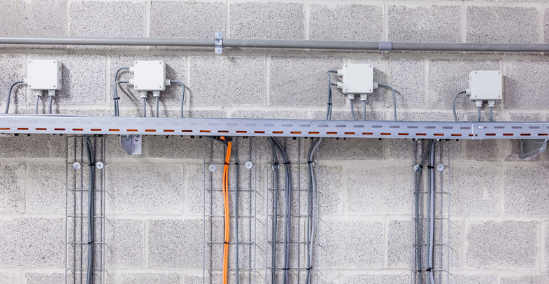
Auch das Chassis selbst ist häufig ein hervorragender Leiter für Störungen. Wenn eine Leitung nah an diesem entlang geführt wird, dann entscheiden sich die Störungen meist für das Chassis und nicht für die Leitung. Wählt man für eine Leitung hingegen die Abkürzung quer durch die Luft, dann wird auch der müde Wanderer (zugegeben kein eleganter Vergleich) gerne diese angebotene Hängebrücke nehmen und das Tal meiden.
🏔 Wenn Sie also bei der nächsten Wanderung das Gefühl haben, zu stören, gehen Sie einfach zurück auf den Wanderweg 😉
Fehler #4: Pigtails – Hauptgrund für EMV-Probleme
Nun kommen wir auf eine Sache zu sprechen, die ich bei über 90% aller EMV-Störungsbehebungen antreffe:
Pigtails – Schweineschwänzchen!
Wenn ich bei EMV-Seminaren am Mini-Frequenzumrichter auf dem Tisch zeige, wie ein 5 cm langer Schirmanschluss gegenüber einer 360°-Rundum-Verbindung um Faktoren höhere Störpegel bewirkt, dann ernte ich immer wieder ungläubige Blicke. Wie kann das sein? Das Ohmmeter zeigt doch den gleichen Widerstandswert an. Wegen ein paar cm!
Am wichtigsten ist der Rundum-Anschluss bei den Verursachern der Störungen. Das sind wohl in 99% der Fälle Antriebssysteme.
Es kommt nicht von ungefähr, dass die namhaften Drivesysteme-Hersteller in ihren EMV-Richtlinien vorschreiben, den Schirm beidseitig 360° anzuschliessen. Pigtails sind klar verboten und machen die CE-Zertifizierung schlichtweg ungültig.
Sind die Störer richtig abgeschirmt, dann verträgt es bei den anderen Leitungen oft die mangelhaften Schirmanschlüsse…obwohl diese grundsätzlich nicht zu empfehlen sind.
Weshalb das so ist:
5 cm Leitung haben eine Induktivität von ca. 50nH. Schon bei einer Störfrequenz von 10 MHz gibt das einen Scheinwiderstand (Impedanz) von mehreren Ohm. Der Kabelschirm kann dadurch die eingekoppelten Störungen nicht mehr sauber zur Erde ableiten und «tanzt» mit der Störung mit. Dieser Tanz ist ansteckend und koppelt auf die anderen Innenleiter sowie benachbarte Leitungen. Ist der Schirm in Bezug zur Störfrequenzen lang genug, dann hat man sogar eine Antenne gebaut und der Kabelschirm strahlt in alle Richtungen ab.
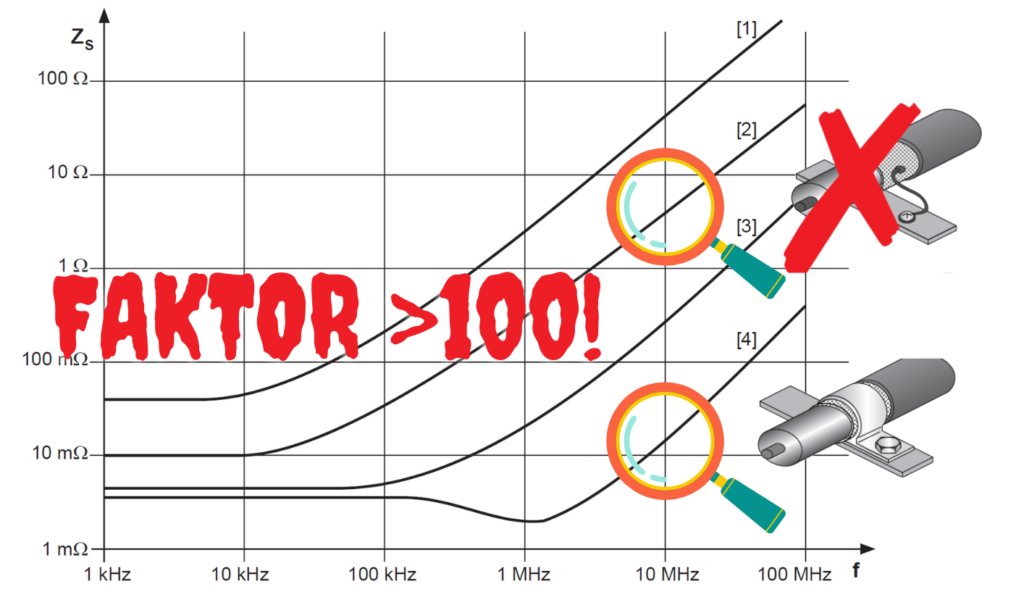
Nach dem Motto: Gut gemeint ist das Gegenteil von gut.
Mangelhaft (oder gar nicht!) angeschlossene Kabelschirme sind damit kontraproduktiv und verschlechtern die EMV-Robustheit eines Systems.
Am EMV-Praxis-Seminar lernen Sie anhand praktischer Beispiele, wie Sie im Maschinenbau für ein robustes EMV-Design sorgen. Ohne unnötig teuren Komponenten, aber mit zielführenden Massnahmen, die wie ein Getriebe sauber ineinander greifen.
Fehler #5: Spaghettata im Schaltschrank
Gratuliere: Sie fahren MIT ABSTAND am besten!
Bestimmt haben Sie das auch schon mal auf dem vor Ihnen STEHENDEN Auto gelesen.
Die häufigste Unfallursache ist Unachtsamkeit und Ablenkung – zusammen mit einem zu kleinen Abstand eine tödliche Mischung.
Es gibt kaum eine Regel, die so einfach zu verstehen ist, und doch so oft gebrochen wird.
Bei der EMV genau dasselbe.
Abstand ist etwas, das bei sämtlichen elektromagnetischen Koppelmechanismen hilft und trotzdem viel missachtet wird.
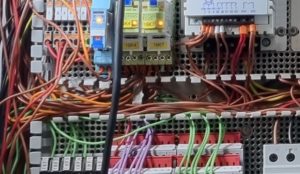
Besonders im Schaltschrank haben wir häufig Platzmangel und tatsächlich gibt es Tricks und Massnahmen, durch welche man auch mit deutlich kleineren Abständen sicher sein kann:
- Leitungen in Klassen aufteilen
- Klassen getrennt führen
- giftige Leitungen richtig schirmen
- metallene Rückwände, Holmen und Kabelkanäle als Schirmung nutzen
Leider gibt es wie im Strassenverkehr auch bei der EMV eine Art Kettenreaktion und schon eine «verseuchte» Leitung am falschen Ort kann alles beeinträchtigen und zu EMV-Problemen führen. Es ist daher wichtig, ein sauberes Design zu machen, auf Papier zu bringen und mit jemandem zu besprechen, der einen erfahrenen Blick dafür hat.
Fehlende EMV-Schulung und Sensibilisierung
Viele Fehler wären früh und einfach vermeidbar, wenn ein praxisorientiertes Grundwissen bei allen Beteiligten vorhanden wäre. Oft sind aber Ingenieure und Elektrokonstrukteure unzureichend sensibilisiert in Bezug auf die Stolperfallen eines EMV gerechten Designs.
Die Folge sind unvorhergesehene Störungen, welche zu Verzögerungen, erhöhten Kosten und Ausfällen führen.
Diese Personen sollten ein Grundlagen-Training in EMV absolvieren:
- Entwicklungsingenieure
- Elektrokonstrukteure
- Automatiker
- Inbetriebnahmetechniker
- Servicetechniker
- Technische Kundendienstmitarbeiter
Diese Themen gehören in ein zweckmässiges Training
- Ausbreitung von Störungen in einer Anlage
- Praxisübungen und Experimente, weil «Begreifen» von «Greifen» kommt
- Verdrahtungsregeln
- Abschirmung und Kabelkanäle
- Erdung und Potentialausgleich
- Netzfilter
- Zonendesign
So gelingt eine nachhaltige Sensibilisierung
- Gemeinsames On-site Training für alle Beteiligten
- Neue Mitarbeiter extern ins Training schicken
- Bei akuten EMV-Problemen oder neuen Designs externen EMV-Experten beiziehen und die Gelegenheit gleich für eine «Schnellbleiche» nutzen.
- Online-Training abonnieren, damit die Mitarbeiter sich regelmässig und kostengünstig auf dem aktuellen Stand halten können.
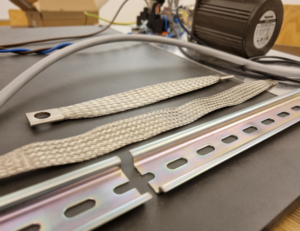
Um Ihr Team optimal auf die Herausforderungen der EMV vorzubereiten, laden wir Sie herzlich zum nächsten EMV-Seminar ein. In diesem praxisorientierten Kurs lernen Sie, worauf es beim EMV gerechten Design von Schaltschränken, Maschinen und Anlagen ankommt. Wir erleben die Realität live am Frequenzumrichter und wenden die entscheidenden Massnahmen direkt an.
Einen Vorgeschmack erhalten Sie am kostenlosen 15-Minuten Livehack. Dort sind sie direkt mit dabei, wenn Störungen eines FUs mit 150€-Messequipment detektiert und sofort behoben werden.
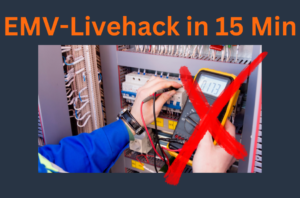
Grundlagentrainings und kontinuierliche Weiterbildung sind der Schlüssel, um EMV-Designfehler zu vermeiden und die Zuverlässigkeit Ihrer Maschinen zu gewährleisten. Planen Sie Weiterbildungen vorausschauend und bringen Sie Ihr Team auf den nächsten Level!