Kennen Sie das? Einige Elektromotoren halten ewig, andere sorgen für ein gutes Ersatzteilgeschäft und missmutige Kunden. Getriebe oder Motoren fallen nach kurzer Zeit aus, obwohl sie mit genügend Reserve dimensioniert sind …
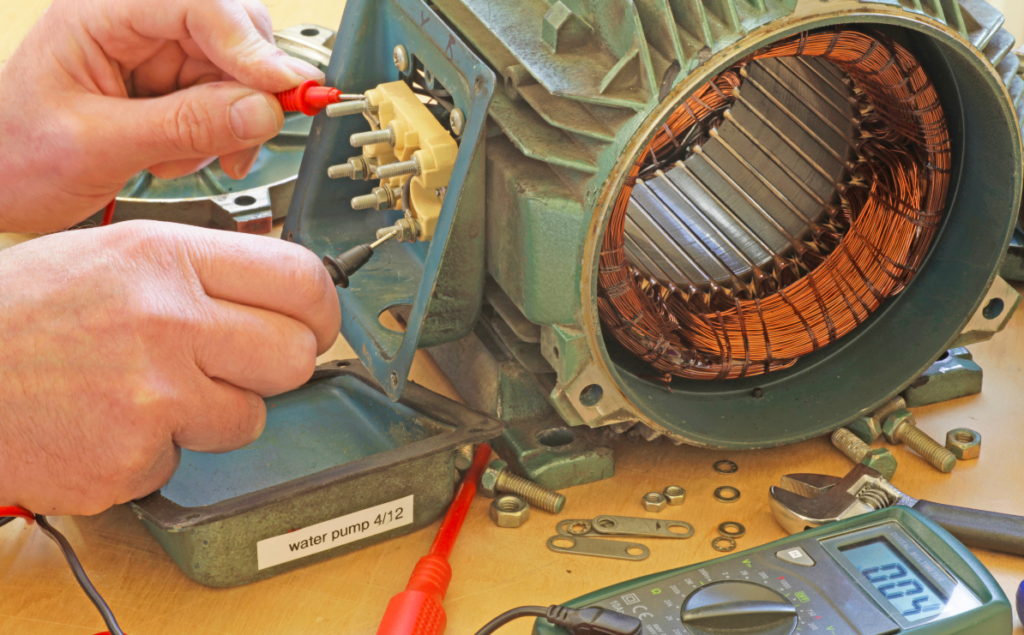
Ob in kleinen Linearantrieben, in Fördersystemen oder gar in grossen Windturbinenparks – das Problem begegnet mir immer wieder, obwohl es unter Spezialisten altbekannt ist und Lösungsmöglichkeiten vorhanden sind.
Könnte es wie so oft daran scheitern, dass Elektro- und Maschineningenieure einerseits mehr miteinander sprechen dürften und andererseits die gegenseitigen Disziplinen besser verstehen sollten?
Kein ersichtlicher Grund
Die Leistungsdaten sind in Ordnung, keine Überbelastung, trotzdem fallen die Motoren immer wieder aus. Weil ersetzen oft günstiger ist als reparieren, schaut man erst genau hin, wenn sich Kunden beschweren oder ein gutes Q-System Alarm schlägt. Leider ist man dann schon in der Serienproduktion, hat die Bestände gefüllt und die Anlagen auf der ganzen Welt verteilt.
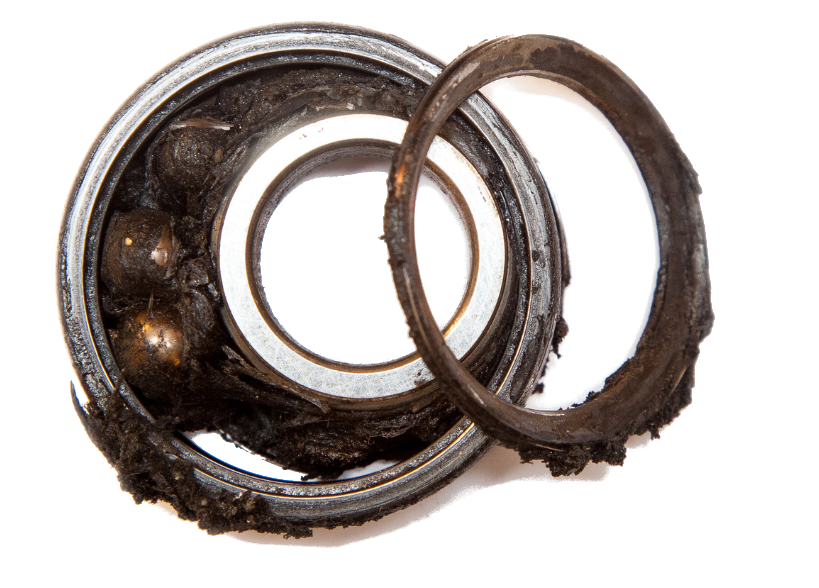
Die Lager sind dann meist so arg beschädigt, dass sich die Ursache nicht mehr eruieren lässt und man bei der Mechanik sucht. Ist die Lagerung der Welle überbestimmt? Sind die radialen Kräfte innerhalb der Spezifikation? Braucht es eine Schwingungsdämpfung? Was ist mit Toleranzen, Temperatureinwirkungen und Materialproblemen?
EMV kann der Grund sein
Nicht selten stammen aber Lagerschäden von elektrischen Strömen, die ungewollte Wege nehmen. Dafür gibt es mehrere mögliche Gründe, die wir gleich etwas genauer anschauen werden.
Wer jetzt denkt, das gehe Maschineningenieure und Konstrukteure nichts an, der irrt. Das Motoren- und Getriebesterben hört erst auf, wenn alle Beteiligten ein Grundverständnis für elektromagnetische Verträglichkeit entwickelt haben.
Wie die Schäden entstehen
Grund I: Stromdichte
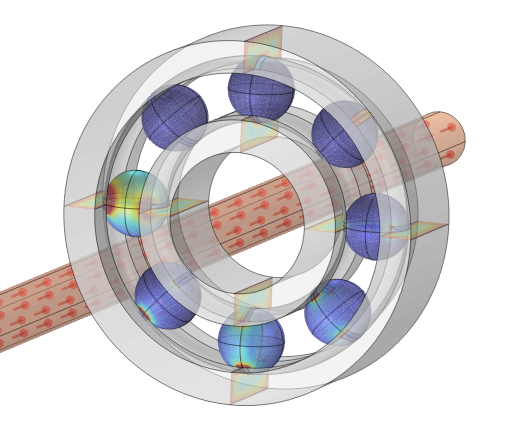
Kugellager oder Wälzlager allgemein beherbergen viele elektrisch leitenden Kontakte mit sehr kleinen Auflageflächen. Was mechanisch toll ist, sorgt elektrisch für eine theoretisch unendlich hohe Stromdichte bei den Kontaktpunkten. Diese Stromdichte sorgt lokal für hohe Temperaturen, welche das Lagerfett zerstören können.
Grund II: Funken
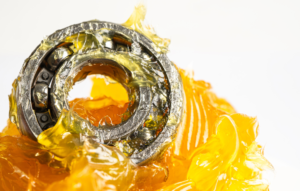
Durch das Fett auf den Kontaktflächen entsteht ein elektrisch isolierender Film, der aber so dünn ist, dass immer wieder Funken durchschlagen können. Durch elektrostatische Aufladungen der isolierten Teile wird dies noch verstärkt und im Funkenmeer beginnt die Erosion des Lagers. Dabei kann die Aufladung durch die Reibung von Antriebsriemen, aber auch durch die kapazitive Kopplung von den Wicklungen stammen.
Dann geht es schnell
Bis zum ersten spürbaren Schaden kann es eine Weile dauern, aber Lagerschäden verstärken sich sofort selbst, weil eine unrunde Kugel zu noch mehr Funken und Verschleiss führt und Materialteile im Schmiermittel den Rest erledigen. Von den ersten (mit Predictive Maintenance eigentlich messbaren) Verschleiss Anzeichen bis zum Stillstand kann es daher schnell gehen.
Woher kommen denn die Ströme?
Induktion
Elektromotoren sind Induktoren. Die Wechselströme in den Wicklungen induzieren auf der Motorwelle eine Spannung. Sobald die Welle mehr als eine leitfähige Verbindung zur Maschine hat, wird diese Spannungsquelle kurzgeschlossen und es fliesst ein Kreisstrom über Welle, Lager und Gehäuse. Dies passiert innerhalb des Motors, aber auch über externe mechanische Komponenten. Solche Ströme können gross sein und die Frequenz entspricht der Drehstromfrequenz des Umrichters.
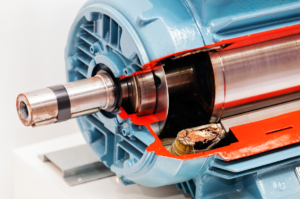
Speziell bei Motoren mit langer Welle kann es hier sinnvoll sein, isolierende Lager oder isolierende Kupplungen einzusetzen. Die Ströme sind immer da und nicht von mangelhaften Verdrahtungen abhängig. Abschirmungen und Filter helfen hier nichts, die induzierten Spannungen werden nur durch die Geometrie des Motors und die elektrischen Parameter Frequenz und Strom bestimmt.
Hochfrequente Gleichtaktströme
Jetzt kommt der Teil, den man nicht unbedingt verstehen, aber zwingend beachten muss!
Je grösser die Energieeffizienz des Frequenzumrichters, desto steiler sind seine Schaltflanken und desto grösser werden die hochfrequenten Anteile, die über die Motorenleitung, den Schirm und das Motorengehäuse abgeführt werden. Diese Ströme müssen zurück zum Netzfilter des Umrichters und suchen sich den besten Weg. Ihre Frequenz ist 1’000…1’000’000 x grösser als diejenige der induzierten Ströme, deshalb gelten hier ganz andere Gesetze.
Es ist wie im Strassenverkehr:
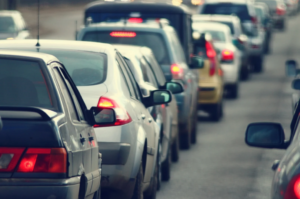
Dort, wo man ihn haben will, muss man für einen guten Fluss sorgen, sonst kommen die Leute mithilfe ihrer Navis auf die verrücktesten Ideen und legen ganze Dörfer lahm. So wie an Ostern also die Autobahnanschlüsse nahe am Gotthardtunnel gesperrt werden müssen, so sollten die heiklen Punkte in einem elektrischen Antriebsstrang unbedingt beachtet werden.
Hat man das EMV-Chaos einmal, dann geht es ohne professionelle Unterstützung kaum mehr weg.
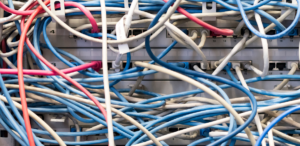
Wie kann man das verhindern?
Wenn der Schirm des Motorenkabels auch nur an einer Stelle und auch nur für 1 mm unsauber kontaktiert wird, hat man verloren.
Dies ist der Fehler Nr. 1, den ich seit 20 Jahren immer und immer wieder antreffe. Der Schirm muss ÜBERALL mit dafür vorgesehenen 360° Verbindungen angeschlossen werden. Funktioniert eine Anlage tatsächlich nur, wenn der Schirm einer Motorenleitung einseitig abgehängt wird, dann sollte der Rückflug des Technikers auf längere Zeit verschoben werden!
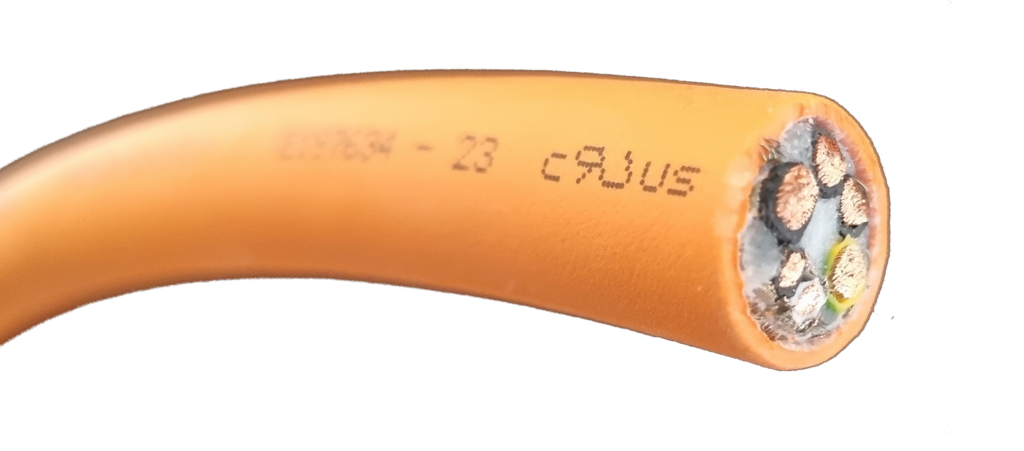
Schirm verdrillen, Schrumpfschlauch drüber und anschliessen, ist ein No-Go!
Ich weiss, wer an das Ohm’sche Gesetz glaubt, kann das nur schwer fassen. Man muss es einmal praktisch erleben, damit es richtig sacken kann. Also unbedingt an mein nächstes EMV-Praxisseminar kommen und es nie mehr vergessen!
Hochfrequente Ströme gehen nicht den kürzesten Weg, wie viele glauben, sondern denjenigen, der das kleinste Magnetfeld aufbauen muss. Was das praktisch bedeutet, ist im kostenlosen EMV-Report beschrieben:
Nicht selten trifft man in Anlagen auch die teilweise vorgeschriebenen Wartungsschalter an, welche die Motorenleitungen bei Bedarf aus Sicherheitsgründen unterbrechen.
Gut für den Menschen, schlecht für die Maschine.
Sobald Frequenzumrichter im Spiel sind, dann müssen hier IMMER die EMV-Varianten der Schalter eingesetzt werden. Hier zu sparen, lohnt sich definitiv nicht.
Wenn also Umrichter, Netzfilter, Kabel und Motor vom Anfang bis zum Ende richtig geschirmt sind, dann sind die hochfrequenten Ströme meistens schon auf einem erträglichen Minimum.
Wenn Goliath unschuldig ist
Nun gibt es Anwendungen, bei denen es nicht so einfach ist, weil beispielsweise ein Hilfsantrieb auf einem rotierenden Teil montiert ist.
Nehmen wir als Beispiel eine Windturbine: Der Frequenzumrichter der Rotorblattverstellung sitzt irgendwo in der Gondel, die Motorenleitungen müssen über Schleifkontakte geführt werden.
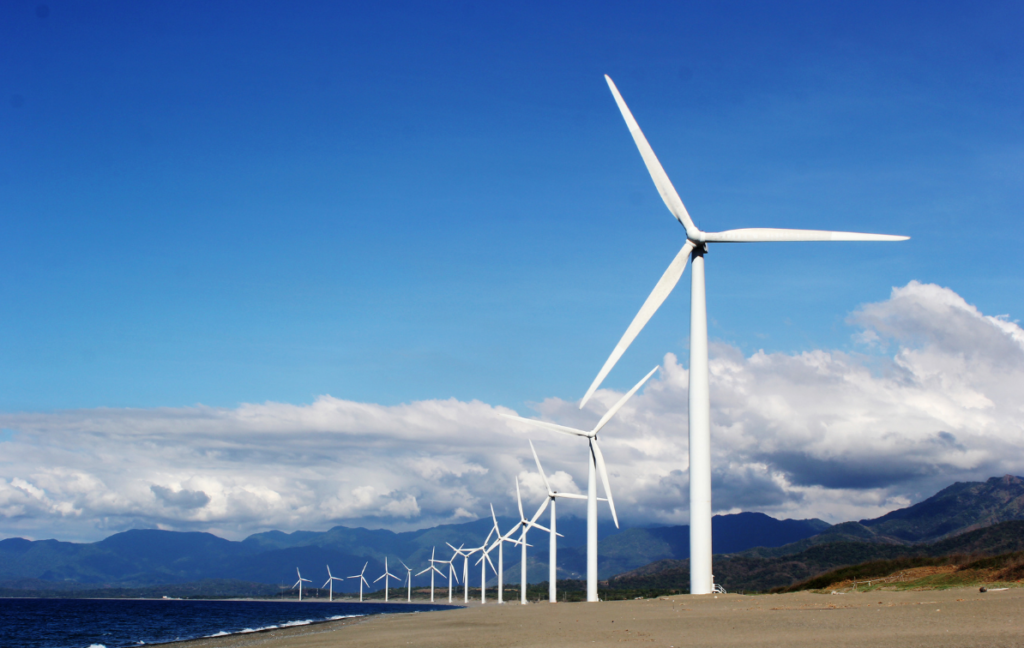
Und der Schirm? Man denkt nun vielleicht, wie nebensächlich dieser kleine Antrieb im Vergleich zu der grossen Maschine ist, aber wo fliessen denn die hochfrequenten Ströme dieser supereffizienten Kleinantriebe durch, wenn die Schirmverbindung nicht wasserdicht ist?
Über das Getriebe des Hauptrotors!
So kann in einem System auch ein kleiner nebensächlicher Störer dazu führen, dass immense Schäden entstehen. Häufig sind die einzelnen Teilsysteme im EMV-Labor geprüft und erst beim Zusammenbau werden die grossen Verbrechen begangen, die dann niemand mehr feststellt. Man versteckt sich hinter übergrossen CE-Labels und den Resultaten aus den Labors.
Und die Spezialisten in der Entwicklung, die eigentlich verstehen würden, was passiert, sind dann schon lange mit der Optimierung des nächsten Produktes beschäftigt. Sie bekommen nichts mehr mit und werden auch nicht gefragt…
Aus diesem Grund richte ich mein Praxisseminar speziell auf Elektrokonstrukteure und Servicetechniker aus. Sie sind es, auf die es ankommt, wenn Labors und Normen im Entwicklungszyklus schon lange der Vergangenheit angehören. Und sie sind es auch, die dann am Ende der Welt in den Anlagen herumkriechen sollen, wenn nichts mehr läuft.
Nochmals zusammengefasst die wichtigsten Punkte
Zwingend
- Geeignete Motorenkabel verwenden (symmetrischer Aufbau)
- Immer geschirmte Leitungen verwenden, Sinusfilter als Alternative nur bei sachgerechter Anwendung.
- Kabelschirm beim Umrichter und beim Motor EMV-sicher anschliessen
- Keine Unterbrechung des Schirms unterwegs ohne spezielle EMV-Komponenten
Optional mit guter Wirkung
- Zusätzliche gute Erdverbindungen über das Motorengehäuse und Anlagenteile nutzen (Flansch blank usw.)
- Bei Rotor-Erdströmen: Isolierung der Motorwelle gegen die Anlage (Hybridlager, Kupplung usw.)
- Bei Funkenentladungen: Rotor-Erdungsringe verwenden
- Common-Mode-Kerne zur Dämpfung der HF-Ströme
Sind diese Basics einmal verinnerlicht, wird es funktionieren. Auch beim nächsten Mal!
Zum Thema EMV gibt’s hier bald ein kostenloses Webinar. Wer nichts verpassen will, kann einfach den Blog abonnieren!